DEVELOPING A CULTURE OF QUALITY BASED ON EFFECTIVE QMS IMPLEMENTATION
- Mar 20
- 3 min read
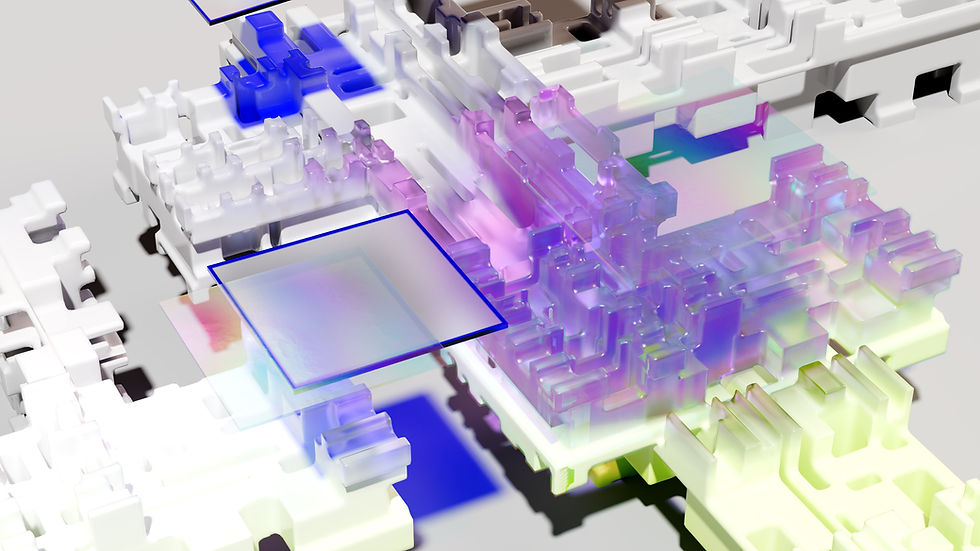
Quality management systems (QMS) are integral to the manufacturing industry, as they play a crucial role in minimizing defects and ensuring the consistent production of high-quality products. The mechanisms through which QMS operates to reduce defects include standardization of process, proactive systems for defect elimination / reduction, and ensuring effective communication pathways between all levels within an organization. Further and key to an effective QMS, understanding the advantages applicable to proactive systems development compared to reactionary responses to quality problems, will ensure long term financial success and growth.
Defining Quality Management Systems
A quality management system is a structured framework that comprises policies, procedures, and processes aimed at achieving quality objectives and continuous improvement at all stages of the product lifecycle. Moreover, these procedures are designed to ensure that every stage of production adheres to specific quality standards, reducing the likelihood of defects and ensures overall product reliability.
One of the core functions of QMS is the standardization of processes. By establishing consistent procedures and guidelines, QMS provides the tools ensuring that all employees follow the same steps and use the same criteria when manufacturing products. This uniformity helps prevent errors and variations that can lead to defects.
QMS also relies on continuous monitoring of production processes through various production controls, metrics and key performance indicators (KPIs). By regularly evaluating these systems, companies can identify potential issues early and implement corrective actions before defects occur. This iterative process fosters a culture of continuous improvement, where minor adjustments can significantly enhance product quality.
Documentation and Traceability
Documentation is a critical component of QMS, providing a detailed record of every aspect of the production process. This traceability allows manufacturers to pinpoint the source of any defects that arise, facilitating swift and accurate resolution. Moreover, comprehensive documentation supports compliance with industry standards and regulations, ensuring that all products meet required specifications.
Employee Training and Engagement
A well-developed QMS emphasizes employee training and engagement, ensuring that all personnel are well-versed in quality standards and procedures at the core of the quality management system. By fostering a sense of ownership and responsibility among employees, training in line with QMS requirements, encourages proactive identification and resolution of potential issues, further reducing the occurrence of operator centric defects and operational inefficiency.
Proactive System Development vs. Reactionary Responses
Anticipating Potential Issues
Proactive system development involves anticipating potential quality issues before they manifest and implementing measures to prevent them. This approach is rooted in thorough risk assessment and strategic planning at the onset of the products lifecycle, allowing companies to address vulnerabilities within their processes preemptively. By contrast, reactionary responses to defects focus on corrective actions only after a problem has been identified, often resulting in higher costs and production delays.
Efficiency and Cost Reduction
The proactive development of QMS is inherently more efficient and cost-effective than reactionary measures. By investing in robust systems and preventive measures, companies can avoid the significant expenses associated with rework, recalls, and customer dissatisfaction. A proactive approach ensures that quality issues are minimized from the outset, reducing the need for extensive corrective actions and costly mistakes.
Building a Culture of Quality
Proactive system development fosters a culture of quality within the organization. When employees are trained to identify and address potential defects early, they become more invested in maintaining high standards throughout the production process. This culture of quality promotes continuous improvement and innovation, driving long-term success and customer satisfaction.
For many businesses quality management systems are vital for developing a culture centered on driving defect reductions and offering a structured framework for achieving consistent product quality. Proactive system development, characterized by anticipatory measures and continuous improvement, is far more effective and efficient than reactionary responses to quality problems. By investing in a robust QMS, companies can foster a culture of quality, reduce costs, and enhance customer satisfaction, ultimately driving long-term success in the competitive manufacturing landscape.
Comments